BUWOG develops new buildings in accordance with environmental, economic and social sustainability criteria. A key aspect in this regard is considering the sustainability of construction materials over the entire life cycle of a building – from initial planning and design to the complete recycling of the materials used. To accomplish this, BUWOG has joined Madaster, a digital library of building materials.
Sustainability in new construction also means considering what future generations might want to do with the buildings after they have been built. How will they deal with the building materials 50 or 100 years from now? Perhaps when the grandchildren of the original owners want to rebuild, modernise, enlarge or demolish the building? This moment of truth may come sooner than expected – as the problem of asbestos, once a popular building material, shows. Still widely used up into the 1990s, today, some 30 years later, asbestos has to be painstakingly located and removed. But even other insulation systems, including those that do not have harmful health effects, do not have an unlimited lifespan and may need to be replaced, upgraded or brought up to the current state of the art after 30 or 40 years of use. And during modernisation works, it is important to know what was used in the past – and where.
The basis for recycling: a digital registry for building materials
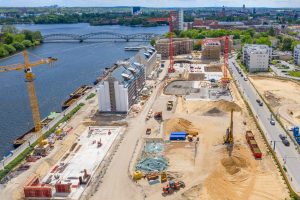
March 2021 saw the creation of Madaster, a digital platform to register, document and archive the materials used in construction. As a central global registry for materials, buildings and infrastructure objects, Madaster simplifies the process of reusing materials, promotes intelligent design and avoids waste. The idea originated in the Netherlands, where around 2,000 buildings are already registered with the platform. In Germany, the launch of Madaster is backed by several companies from the real estate sector. BUWOG, for example, is on board as one of the largest private residential real estate developers.
BUWOG Managing Director Eva Weiß: “We are convinced that our business model can only be viable for the future if it is operated sustainably and in a resource-saving manner. Madaster offers us the possibility to register materials used in construction so they can be reused later in our own projects or externally.” Specifically, that means that the building materials to be used, along with their technical specifications and their composition of various raw materials, are registered and digitally documented as early as the planning stage – from the type of concrete and the insulating materials to the cables or electrical wiring that are later concealed under plaster and no longer visible. The registration lays the groundwork for the future. If, for example, electrical cables need to be replaced 20 or 30 years down the road, the material registry shows exactly what was used before. This makes it much easier to separate, collect and recycle products, and with the online materials library, building materials can be put to new uses. “This makes Madaster an important building block on the way to a circular economy,” Eva Weiß explains.
New life for old buildings
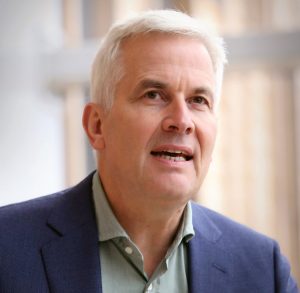
Admittedly, there still is a long way to go. But people have become aware of the issue, and the real estate sector is determined to deepen its participation in the circular economy. The German construction sector still produces around 230 million tonnes of construction and demolition waste every year, which corresponds to about 55 percent of the total gross waste generation. “Considering the challenges that lie ahead in terms of climate, energy and raw materials, change is necessary. And digitalisation is an important driver for the transition in the construction and real estate sector,” explains Thomas Rau, co-founder of Madaster. In order for society and the environment to benefit quickly, as many players in the real estate industry as possible must now follow suit.
Until then, managing demolition waste remains feasible, but much more complex. This also holds true for BUWOG’s construction sites, where great efforts are already being made to recycle used material. During the demolition of a run-down 1930s warehouse building in Berlin-Spandau, for example, a special grapple was used to dismantle the old building and carefully remove the pieces bit by bit. As it was not clear which materials had been used 90 years ago, however, and this had not been recorded anywhere, the waste had to be thoroughly examined and tested by specialist companies. The materials were then sorted before being stored and taken away separately. In this way, bricks, concrete, metals, etc. could be recycled as effectively as possible.
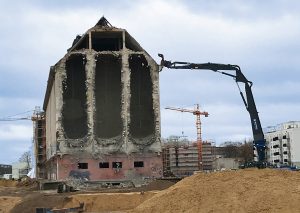
Of course, it would be ideal if buildings didn’t have to be demolished at all but could be skilfully refurbished and redesigned for future use, says BUWOG Managing Director Eva Weiß: “Wherever possible, we try to refurbish existing buildings, make them fit for residential use and integrate them into our mixed-use developments.” On the construction site in Spandau, this is exactly what was achieved with two of the three warehouse buildings on the banks of the Havel. These buildings are currently being renovated and redesigned to create 82 condominiums. A further 262 rental apartments are being built on another construction site along Parkstraße. This project involves the construction of three buildings with a rainscreen façade system made of trapezoidal aluminium cladding sheets. The façade can be completely dismantled, reused and recycled. The aluminium itself consists to a high degree of recycled material.
Prices for raw materials on the rise
The materials registry is not only good for the environment but also has economic benefits. After all, prices for construction materials, whether sand, concrete, metals or wood, are on the rise. “Our planet is a closed system, so the supply of raw materials is finite,” explains Thomas Rau, co-founder of Madaster. “We need to keep these finite materials infinitely available. And we can achieve this by giving the materials a documented identity. Material without identity is waste. Our platform enables the infinite reuse of materials, with buildings acting as material repositories. We write materials down rather than writing them off.”
In the coming months, Madaster and its partner companies, including BUWOG, will be further expanding the network in Germany – laying the foundation for the circular use of products and materials in the construction industry.
“Madaster an important building block on the way to a circular economy.”
The Madaster partner network
Madaster sees itself as part of an entire ecosystem consisting of science, product manufacturers, the recycling industry and other digital platforms. Partners include Commerz Real, Drees & Sommer, Interboden, Edge Deutschland and Vonovia. Even property owners can participate in Madaster with a web-based “material passport”.
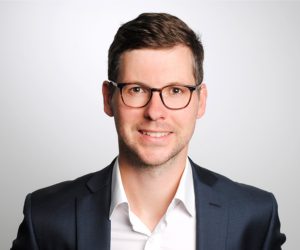
Dr. Patrick Bergmann, managing director of Madaster Germany: “The material passport contains information about the quality, origin and location of materials and provides insight into the material, circular and financial value of a building.” This makes it possible to utilise buildings and infrastructure as material repositories – and, above all, to manage the additional material values of real estate and infrastructure and use them for accounting purposes or real estate valuations.
More information is available at www.madaster.com