“BUWOG in Dialogue” is a discussion format that BUWOG has already established in Vienna as a platform for topics relating to urban development, construction and architecture. The event series now regularly invites people to exchange ideas with representatives from the areas of business, politics, administration and science in Berlin as well. The kick-off event focused on serial and modular construction with timber.
Premiere at the Ludwig-Erhard-Haus in Berlin: Daniel Riedl, member of the management board of Vonovia responsible for BUWOG development in Germany and Austria, welcomed the following guests to the podium for the first Berlin event in the “BUWOG in Dialogue” series: Sun Jensch, managing director of the Coalition for Timber Construction (only in German), Eva Weiß, managing director of BUWOG Bauträger GmbH, Prof. Dr. Katharina Kleinschrot from TU Dresden and Markus Fuhrmann, CEO and co-founder of GROPYUS, a PropTech company that plans to revolutionise residential construction through digital and serial timber hybrid construction.
“Assembly line work”: one finished component every 17 minutes
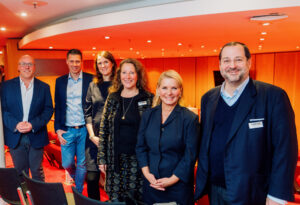
Fuhrmann opened the panel discussion by presenting the technological and industrial approach of GROPYUS. The company develops and builds sustainable apartment buildings using serial and modular timber-hybrid construction methods and offering turnkey solutions from a single source. The key aim is to reduce construction costs and shorten construction times by as much as 50 percent. This is achieved through digital processes and modular production. The GROPYUS smart factory in Baden-Württemberg is home to industrial production lines with 50 robots that manufacture wall and ceiling elements. It takes just 17 minutes for a wall element to roll off the production line.
What’s more: GROPYUS aims to make residential buildings not only affordable and sustainable – but also intelligent. “We think in terms of building life cycles,” says GROPYUS CEO Markus Fuhrmann. This includes not only planning, production and assembly, but also what happens to the building when it is finished. A building operating system developed by GROPYUS becomes a digital control and communication centre that not only facilitates the seamless integration of smart home functions for greater residential comfort, but also offers extensive applications for facility, property and asset management. These include predictive maintenance based on system status data, automated billing management for rent and ancillary costs as well as continuous cost optimisation using data analytics.
Less regulation, uniform laws: what policymakers have to do
Lower-cost, faster construction, resource-conserving and environmentally friendly through the use of renewable raw materials and optimised cost-effectiveness through efficient building management – a win-win strategy for residents and the housing industry alike. But what are the obstacles? What is preventing the housing industry from more systematic, serial and modular timber construction?
One especially pressing obstacle is the number of deficits in building regulations, Sun Jensch points out. She is the managing director of the Coalition for Timber Construction, an initiative that is committed to building with timber. According to Jensch, timber construction is political and the hurdles that stand in the way of timber construction are political. “Policymakers have already recognised that serial and modular construction is one way to emerge from the crisis in residential construction crisis,” Jensch says. Now they have to deliver: Legislators should facilitate serial and modular construction with timber as quickly as possible.
The fact that there are 16 different state building regulations in Germany is proving to be a stumbling block. The construction industry has long called for standardisation. According to Eva Weiß, managing director of BUWOG Bauträger GmbH, planning starts from scratch as soon as a national border is crossed. “This is an issue that we are trying to get a handle on,” says Weiß. And that is by way of type approvals. “We are currently in close dialogue with the Ministry of Construction in Saxony to have a GROPYUS building approved. In other words, not just a building, but the system as a whole.” If this is successful, it would be possible to roll out lower-cost, sustainable serial and modular construction with timber on a large scale within the Group.
BUWOG and its parent company Vonovia have entered into a strategic partnership with GROPYUS. The aim is to jointly develop and carry out timber construction projects in Germany and Austria. In Berlin, the first prototype has launched, the so-called Basishaus (“base structure”), where 27 rental apartments are being built in serial and modular timber frame construction.
Timber construction: encouraging acceptance and gathering experiences
Timber construction is still struggling with an entire range of prejudices, however, says timber construction expert Sun Jensch, whether woodworm, a lack of fire protection or problems with mould. When building in series, there is also the accusation of a lack of aesthetic individuality. According to GROPYUS CEO Markus Fuhrmann, however, these issues can be nearly all but ruled out with today’s technical possibilities. “Instead, the advantages outweigh the disadvantages, such as a much better and healthier indoor climate,” says Fuhrmann.
The accusation of a lack of individuality can also be refuted. According to Eva Weiß, it is important to remain within the construction standards for serial and modular construction. When it comes to façade endings, floor coverings, etc., modifications and variations are possible and necessary. This means that a serially constructed building can be standard yet still have an individual look.
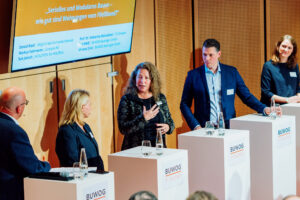
However, the lack of acceptance of timber construction is also noticeable in another sphere: “We need more architects who tackle the topic of timber construction and acquire experience and references in it,” Jensch explains. One example: For every public tender, an architectural firm must present six completed reference projects. “But,” Jensch asks, “where are these supposed to come from?”. Only around 2.5 percent of the total project development volume in multi-storey residential construction is currently being realised in timber construction, although everyone’s been talking about the issue for at least two years. “By comparison within Europe, Germany is last when it comes to building with prefabricated elements,” Prof. Dr. Katharina Kleinschrot from TU Dresden adds. In every other country, serial and modular construction – including conventional construction methods – is far more common.
Modular and serial construction: a chance for greater circularity and sustainability
More efficient, faster, more cost-effective – the advantages of systemic and serial construction are obvious. Prof. Dr. Katharina Kleinschrot would also like the focus to be on circularity, i.e. the end of a building’s life cycle. She broadens the view and emphasises that serial and modular construction is not limited to timber as a raw material. The construction method is extremely important in terms of circularity. The topic can also be applied to elements of technical building equipment (TGA) and reinforced concrete construction. In a systemically constructed building, the dismantling and recycling of raw materials is much easier to implement, because “everything we standardise can be separated and reused much more easily,” says Prof. Dr. Kleinschrot, who specialises in construction and process engineering and circular value creation.
Serial and modular construction with timber not only opens up new opportunities for the housing industry but also represents a key step towards greater sustainability and resource efficiency. The technological advances and focus on circularity not only offer advantages in the construction phase, but also throughout the entire life cycle of a building. However, in order to realise the full potential of this construction method, the underlying policy framework, social acceptance and the development of corresponding skills are critical in addition to technical innovation.